Program Coordinator/Welding Instructor
- FMA
- The Fabricator
- FABTECH
- Canadian Metalworking
Categories
- Additive Manufacturing
- Aluminum Welding
- Arc Welding
- Assembly and Joining
- Automation and Robotics
- Bending and Forming
- Consumables
- Cutting and Weld Prep
- Electric Vehicles
- En Español
- Finishing
- Hydroforming
- Laser Cutting
- Laser Welding
- Machining
- Manufacturing Software
- Materials Handling
- Metals/Materials
- Oxyfuel Cutting
- Plasma Cutting
- Power Tools
- Punching and Other Holemaking
- Roll Forming
- Safety
- Sawing
- Shearing
- Shop Management
- Testing and Measuring
- Tube and Pipe Fabrication
- Tube and Pipe Production
- Waterjet Cutting
Industry Directory
Webcasts
Podcasts
FAB 40
Advertise
Subscribe
Account Login
Search
The importance of welding procedure specification (WPS)
The Last Pass weighs in on documentation for end-to-end welding processes
- By Greg Siepert
- March 21, 2024
Last time, I discussed the need to clarify the acronyms and abbreviations we use within our specific industries. I made this statement at the end: “I hope I can help those working their way into the industry understand the importance of the hierarchy of a paper trail, how and when to use correct terminology, or why we might need a WPS—I mean, a welding procedure specification—for a specific weld.”
That statement generated the following comment: “What is so important about having a WPS? I have worked for years, I set the machine to my favorite settings, and I weld.” I will try to clear the muddy waters and address why a WPS is important. Bear with me as I try to unpack a tremendous amount of information in a small space.
There are essentially two types of welds: those that fall under a specific code and those that do not. However, this discussion is not about code use but rather the importance of the WPS used within various welding codes. We will be looking at welds governed by a welding code.
For those unfamiliar with the process, in the broadest of explanations, a code book will include proven techniques, pre- and postweld evaluation processes, design requirements, and weld process requirements, among many other things. By design, these codes meet a vast spectrum of applications. Some may be broader, while others are material-specific, industry-specific, or application-specific. Depending on the code or codes used, the requirements will cover all aspects of the weld from start to finish.
Various levels of documentation make up the paper trail of a completed weld. Often referred to as the “recipe for the weld,” the WPS contains the information the welder needs to follow regarding amperage, voltage, polarity, electrode, filler metal specifications, base metal specifications, applicable joint designs, travel direction, and weld sequencing.
The thing to remember in this whole hierarchy of welds and documents is that if done correctly through code-required testing, a WPS is based on facts from successful welds. These successful tests are recorded in the procedure qualification record (PQR). Welds done for a PQR will undergo various destructive and possibly nondestructive testing. If successful, the WPS is generated and used for qualifying welders and with welds as outlined in the project.
So, back to the original question: Why is a WPS important? To answer this simply, companies often work under contractional obligations dictated by the scope of work, municipality, or agency as a contract requirement. When a contract requires a specific code, the code will dictate WPS usage. Failure to use a WPS on a project that requires it is a risk that could lead to job loss, fines being levied against your employer, or a host of other issues.
subscribe now
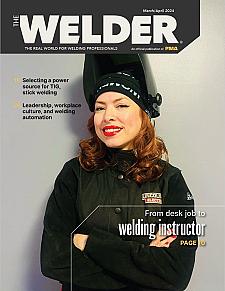
The Welder, formerly known as Practical Welding Today, is a showcase of the real people who make the products we use and work with every day. This magazine has served the welding community in North America well for more than 20 years.
start your free subscriptionAbout the Author
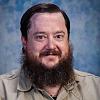
Greg Siepert
Hutchinson Community College
1300 N Plum
Hutchinson, KS 67501
About the Publication
- Stay connected from anywhere
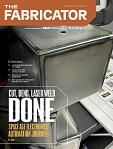
Easily access valuable industry resources now with full access to the digital edition of The Fabricator.
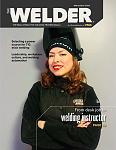
Easily access valuable industry resources now with full access to the digital edition of The Welder.
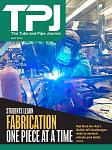
Easily access valuable industry resources now with full access to the digital edition of The Tube and Pipe Journal.
- Podcasting
- Podcast:
- The Fabricator Podcast
- Published:
- 04/16/2024
- Running Time:
- 63:29
In this episode of The Fabricator Podcast, Caleb Chamberlain, co-founder and CEO of OSH Cut, discusses his company’s...
- Trending Articles
Sheffield Forgemasters makes global leap in welding technology
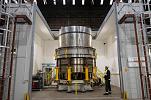
ESAB unveils Texas facility renovation
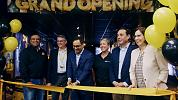
Engine-driven welding machines include integrated air compressors
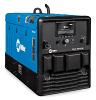
The impact of sine and square waves in aluminum AC welding, Part I
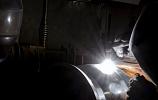
How welders can stay safe during grinding
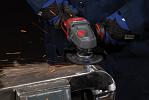
- Industry Events
16th Annual Safety Conference
- April 30 - May 1, 2024
- Elgin,
Pipe and Tube Conference
- May 21 - 22, 2024
- Omaha, NE
World-Class Roll Forming Workshop
- June 5 - 6, 2024
- Louisville, KY
Advanced Laser Application Workshop
- June 25 - 27, 2024
- Novi, MI