Senior Editor
- FMA
- The Fabricator
- FABTECH
- Canadian Metalworking
Categories
- Additive Manufacturing
- Aluminum Welding
- Arc Welding
- Assembly and Joining
- Automation and Robotics
- Bending and Forming
- Consumables
- Cutting and Weld Prep
- Electric Vehicles
- En Español
- Finishing
- Hydroforming
- Laser Cutting
- Laser Welding
- Machining
- Manufacturing Software
- Materials Handling
- Metals/Materials
- Oxyfuel Cutting
- Plasma Cutting
- Power Tools
- Punching and Other Holemaking
- Roll Forming
- Safety
- Sawing
- Shearing
- Shop Management
- Testing and Measuring
- Tube and Pipe Fabrication
- Tube and Pipe Production
- Waterjet Cutting
Industry Directory
Webcasts
Podcasts
FAB 40
Advertise
Subscribe
Account Login
Search
A deep dive into a bleeding-edge automation strategy in metal fabrication
How sheet metal automation drives Space Age Electronics forward
- By Tim Heston
- May 7, 2024
- Article
- Automation and Robotics
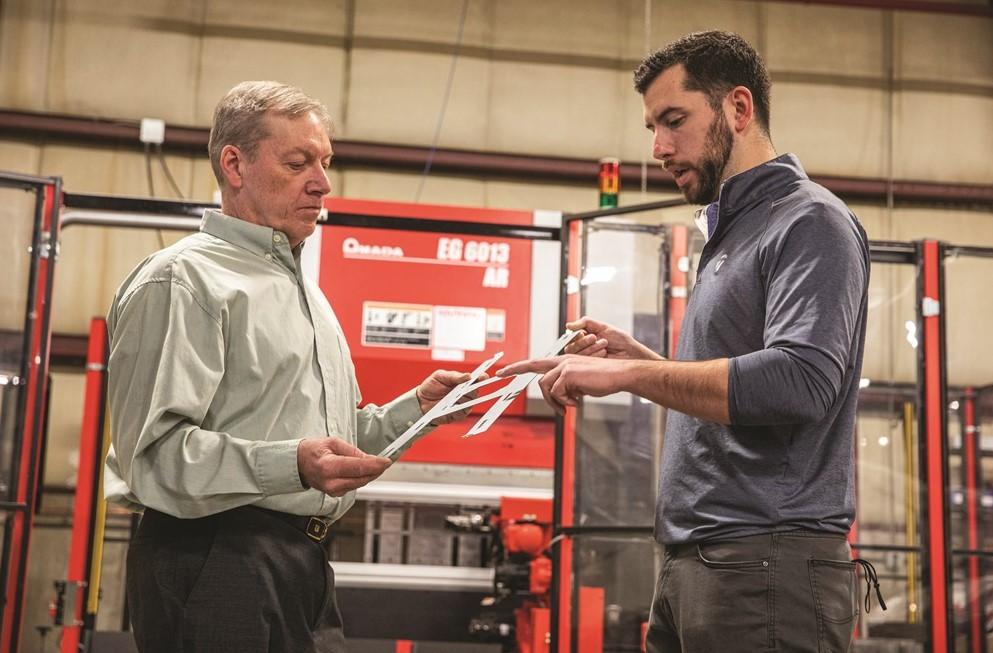
FIGURE 4. (From left) Joe Mongeau, president, and Ryan Mongeau, director of technology, inspect “the claw,” an intricate ceiling bracket formed on the robotic brake. AMADA AMERICA
Earlier this year, Ryan Mongeau inspected an unassuming metal box—16-ga. formed and welded 1008 cold-rolled steel, 4 in. tall and deep, 3 in. wide. No big deal, right?
The weld didn’t look conventional, though. It certainly wasn’t MIG, but it wasn’t TIG either. It was, in fact, an autogenous, conduction-mode laser weld, which a robot performed to perfection over a half-lap joint (see Figures 1 and 2). Part of a fire alarm appliance to be mounted on the outside of a building, the box required no grinding or any other secondary operation. Even the corners were shiny and smooth. After welding, that box went straight to powder coating, then final assembly.
Installed earlier this year, the AMADA laser welding robot represented Mongeau’s latest project in an automation journey that’s only seven years old. During that time, the director of technology at Space Age Electronics has spearheaded a company-wide automation effort that’s been central to the manufacturer’s growth in recent years: automated blanking and part removal, automated bending, and now robotic laser welding.
The Sterling, Mass.-based manufacturer of fire-alarm and life safety products has seen revenue grow by more than 40% since 2017. Its systems can be found in various commercial structures, from office buildings to stadiums, including Fenway Park.
“We recently finished the largest year ever in the company’s history,” Mongeau said. “Even through COVID, we didn’t see a drop in business.”
Some fabricators spend years testing the automation waters. A high-volume job calls for a welding robot, maybe even a robotic bending cell—but the automation initiative starts and ends with that job. Overall, the fabricator’s wide range of part volumes and demand cycles simply do not justify an entire operational overhaul, at least that’s how the thinking goes.
Space Age has taken a different approach. Company leaders see manufacturing strategy and business development as two sides of the same coin. It employs experts both in life safety product development and manufacturing, including manual and automated processes. That intersection of skill represents the organization’s true competitive advantage.
Lessons Learned From Robotic TIG
At 80 employees, Space Age isn’t a massive company, but its automation strategy has allowed it to scale like one, especially in its precision sheet metal fabrication department. Company engineers have learned to perfect the way grippers lift parts from the punch/laser combo, bend pieces large and small on its two robotic press brake cells, all from AMADA. The idea is to make best use of talent. The last thing managers want is for good people to become bored and fatigued from repetitive tasks: denesting, bending, and welding the operation’s higher-volume jobs.
For years, Space Age operated as a very different organization. Mongeau’s grandfather Eugene Mongeau launched the company in 1963 as an injection molding job shop that made trajectory switches and a variety of other components for rockets and missiles (hence the company’s “Space Age” moniker). A few years after the founding, Eugene Mongeau developed the industry’s first audio-visual fire alarm panel, a product that put Space Age in the fire alarm systems industry. Today, the operation makes a wide range of life safety products, including control panels for sophisticated smoke control systems that evacuate smoke during a fire. Some of its latest products include area of rescue (AOR) systems, providing a communication lifeline during intrusion events. (Such products serve a market need that stems from an unfortunate reality in an era of mass shootings.)
“Our manufacturing environment involves a lot of high-volume, low-mix work, but we also have a lot of high-mix, low-volume work. It’s never consistent from day to day, so we need to be able to pivot at a moment’s notice.”
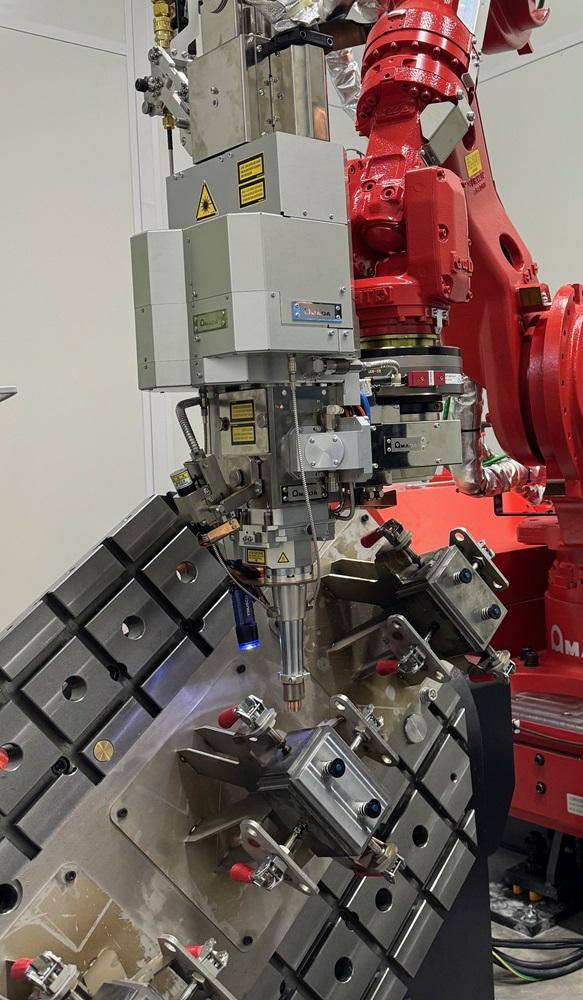
FIGURE 1. A fiber laser welding robot prepares to perform a conduction seam weld on a half-lap joint, from precision-cut and -formed flanges with automated blanking and bending. Fixturing keeps the flange positions to within ±0.005 in. Space Age Electronics
That was Joe Mongeau, company president, Mongeau’s father, and the second generation to lead the family business. “In the beginning, sheet metal was consistently outsourced except for a small prototype shop. We started with a hand punch and leaf brake. By the 1990s and early 2000s, we had multiple CNC machines, and from there we started moving forward,” Joe Mongeau continued.
Until 2017, the organization had a typical CNC sheet metal department, full of punch presses, brakes, and welding cells—mostly TIG, which suits the thin material and customer-facing, cosmetically critical weld joints the fabricator needs to produce. That year, the operation made an unusual first move into sheet metal fabrication automation, with the purchase of a TIG welding robot. The company needed to seam-weld thin sheet metal to produce a weather-proof, visually appealing seal. TIG welding had been Space Age’s process of choice for years, so automating it seemed like the next logical step.
“To be honest, it wasn’t the best solution for us,” Mongeau conceded. “It was a bit of an experiment for us, a way to gain experience with robotic operation.”
Challenges remained with fixturing, fit-up, and distortion. The robot wasn’t equipped with seam tracking, and issues arose with excessively large heat-affected zones that contributed to warping. Company engineers experimented with robotically welding some workpieces part way and then having TIG welders finish the job. Nothing seemed to work entirely as expected, an issue that eventually led to integrating an AMADA fiber laser welding robot in 2024.
Mongeau held up an unassuming box that’s now being welded with a fiber laser. To someone outside fabrication, a half-lap corner joint for an enclosure or box looks utterly ordinary. To someone who bends or welds for living, though, a box can be an impressive sight, especially if it’s formed to create a zero-gap joint with a minimal weld notch. A dialed-in program at the bending robot can make this happen. At the welding robot, a fixture with a series of toggle clamps and laser-cut components holds the piece to within a tolerance less than ±0.005 in.
“There is some variability in material, of course,” Mongeau said, “especially as we shift from one lot of steel to another. But it’s all accounted for in the fixture, which allows us to pull everything nice and tight.”
Of course, a lot happened between that first TIG welding robot and its latest fiber laser welding system. Space Age’s journey from welding through both blanking and bending automation shows just how tightly integrated the three primary fabrication processes are. No one process can be perfected in a vacuum.
Purchasing, Scheduling, and Flow
Flatness matters. Today, if company managers see issues with specific heats of material, they get on the phone with the steel supplier. Issues can include distortion after cutting, as internal material stresses force a blank to curl slightly. That can wreak havoc on any operation, and especially one relying so heavily on automation.
“In fact, we try to eliminate the possibility before such material even reaches the automation,” Mongeau said, “whether it’s in blanking, bending, or welding.”
The company keeps an eye on global efficiency, not just the local efficiency of a particular workcell. Local efficiency matters, but only in a broader context. Without a holistic strategy, some incredibly advanced fabrication technologies can turn into bottleneck-feeding machines. Processing speeds skyrocket in cutting, bending, or welding, but overall throughput doesn’t budge.
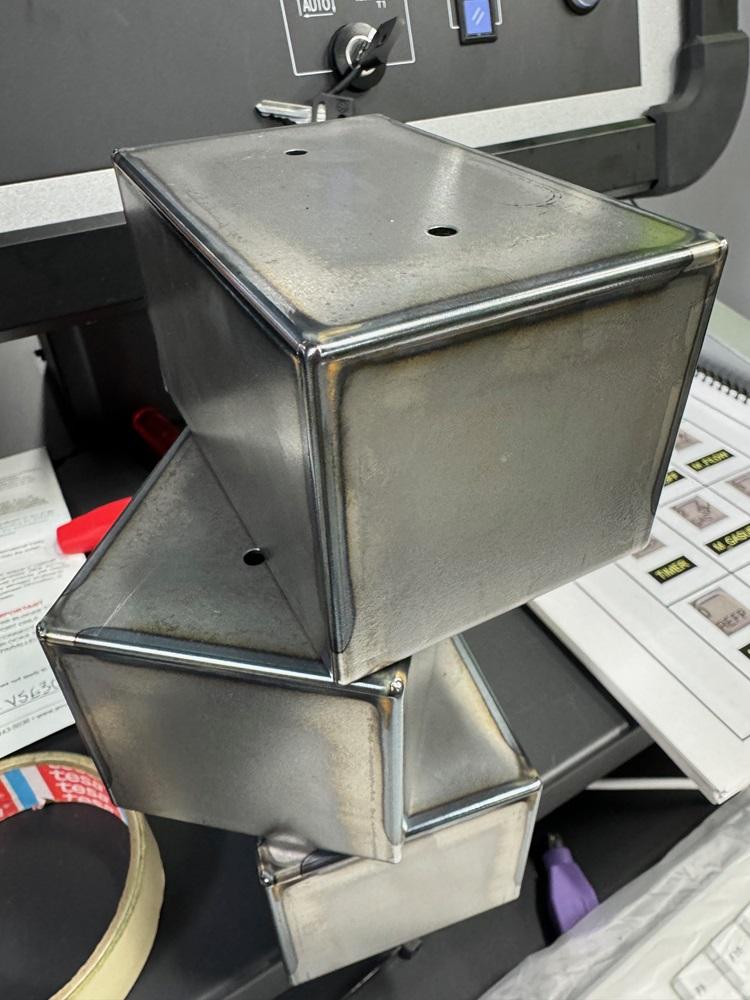
FIGURE 2. Workpieces in the as-welded condition. Requiring no grinding, the boxes head straight to powder coating. Space Age Electronics
This hasn’t been Space Age’s experience. In fact, its overall throughput has gone through the roof. Attribute this to careful planning. “Within our ERP system, we’re constantly looking at inventory demand and supply,” Mongeau said. “We have so many different product lines. It’s not as if we’re making the same thing every single day. If I look at my queue of jobs, we can have as many as 700 different parts that need to be manufactured.”
At first glance, this doesn’t sound like an optimal situation for automation, until you dive a little deeper into the product mix: a select number of high-volume runners alongside a long tail of low-quantity parts. Those high runners provide significant revenue, and so they need to be prioritized, but they also can cause significant headaches and tie up valuable talent on repetitive tasks. Issues with a large order have serious ripple effects, sending behind a host of other, usually lower-quantity orders.
This prevents a high-product-mix operation from effectively scaling up. Shops can streamline changeovers and reduce batch sizes to get closer to that ideal single-piece part flow. But more changeovers also drain machine capacity.
Today, Space Age has automated the high-volume orders that previously tied up the shop’s bending and welding talent. Automation has allowed for strategic batching. The automated punch/laser combo might cut and stack parts all night. Its two bending robots will run unattended for hours, and the same now happens for fiber laser welding. Programs are dialed in so that changeover can happen quickly, allowing production to ramp up and down as needed. Most important: The automation takes those high runners out of the manual fabrication value stream.
“It’s a balancing act,” Mongeau explained. “We want to be lean. We don’t want to carry too much work-in-process inventory. But I also need to make sure we’re maximizing our production time, to ensure the rest of the plant is producing as much as possible.
“We look at our manufacturing from top to bottom, and the fabrication is at the bottom,” he continued. “It all starts from raw material, and we need to produce the fabricated subassembly, which feeds the rest of the plant.”
Space Age views its fabrication capacity as the foundation upon which its other value-added processes are built, from printed circuit board production to wiring, final assembly, and shipping. The right number of fabricated subassemblies must be ready for downstream operations. So, what’s the right number?
“Our system is constantly looking at demand, and it makes recommendations based on an algorithm we’ve developed,” Mongeau said. “This helps us determine what we should be building versus what we shouldn’t be building. And on an annual basis, we go back and look at the algorithm and refine it as necessary.”
Fabricating the Claw
Mongeau described one high-volume product—the TCC Clawed Ceiling Bracket, which starts as an 18-ga. H-shaped blank, with narrow legs each 24 in. long. At the end of each leg are a set of teeth (the “claw” of the product) that, for anyone running a cutting machine with automated part removal, would raise some eyebrows. How could an automated part removal system lift the piece from the skeleton without interference?
In this case, the part design presented opportunity. The “claws” of the product had a flange bent to a 45-degree outside angle. The flange itself presented gauging challenges on the press brake; teeth geometries don’t provide the most rigid, repeatable surface for the brake’s backstops, especially when a bending robot is manipulating the part.
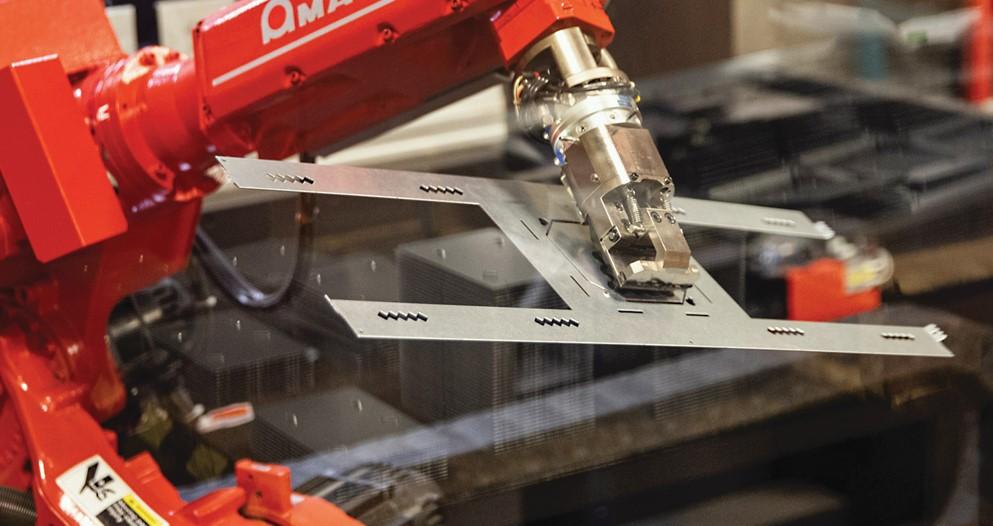
FIGURE 3. A bending robot manipulates a “clawed” ceiling bracket. The narrow “toothed” flange at the right was formed on the punch/laser combo. This made automated part removal in blanking easier and simplified the bending sequence and gauging strategy at the robotic brake. AMADA AMERICA
Those flanges didn’t have to be formed on the brake, though. In fact, they could be formed on the punch/laser combo—a solution that killed two manufacturability issues with one stone (or punch hit). Once the punch form tool created the flange, the teeth were “lifted” out of the skeleton, eliminating all those potential snag points for the part removal automation. It also eliminated a tricky gauging sequence for the bending robot. And because the bend is open, at only 45 degrees, it stacks neatly on a pallet, ready for the bending robot to grasp (see Figures 3 and 4).
Streamlining the Bending Cycle
“It’s like an ongoing kaizen project,” Mongeau said. “When we automate a process, I work with the programmer and engineer, we go through simulation cycles, and within a few weeks or months we’re trying something different. We’re always asking, ‘How can we do this better?’”
Today, simulation can bring a part through every stage of a bending cycle on a robot. Programmers can simulate different grippers, bend sequences, and tooling strategies. Over time, Space Age programmers have learned to analyze that simulation and find ways to optimize the process. A tweak in a gripper design, for instance, can help better secure a part, while strategic rotations can help a robot move from bend to bend without ever letting go. A robot visiting a repositioning station once or multiple times prolongs the bending cycle. If a robot never lets go, it never loses its home position, allowing it to move steadily from bend to bend (see Figure 5).
Bend sequence matters for accuracy, of course, but as company programmers have learned, gravity plays a big role, too, especially when bending larger workpieces. Space Age gained this insight shortly after it invested in its latest AMADA robotic press brake cell with a 10-ft. bed. No bend program can defy physics. Depending on their geometry, some large, thin blanks will bow slightly as the robot manipulates them. To account for this, the robot carefully positions the first bend so that, before the brake ram descends, the blank sits precisely flat on the die shoulders. Humans do this naturally, but for large or long workpieces, at least, a robot’s program needs to account for this.
Whenever practical, the initial bend occurs along a large part’s longest flange. That long first bend makes the part rigid and reduces (usually eliminates) gravity’s effect for the rest of the bend sequence. “Once everything is flat on the tools, I make that first bend,” Mongeau said, “and then, after that, with the part rigid, we can really speed things up.”
Part Removal From the Combo
Automated part removal from the punch/laser combo has helped keep a steady drumbeat of blank production, but as company programmers have learned, the process also requires careful attention to detail. Sharp corners can cause issues—consider the serrated edge of the “claw.” Square corners can be important, too, for reliable gauging at the bending robot, something programmers factor in when creating those mini-nests that ease part removal (see Figure 6).
For most blanks with 90-degree corners (or less), programmers cut an additional gap into the skeleton, usually between 0.003 and 0.004 in., so the parts can be lifted without interference. Laser cutting kerf clearance also needs to be considered, especially since the width of a laser cut is a lot narrower than the gap left by a punch tool. Specific cutting toolpaths help give those edges more clearance, so they lift out without issue.
Perhaps even more important is the sequence that those cuts occur. Because the sheet moves, automated part removal must occur immediately after a part is cut out of the skeleton. How that skeleton takes shape depends on which parts are cut and removed first, and that sequence can have a big impact on the process.
Parts aren’t removed and transported over other parts in the nest, to avoid the possibility of collision. Beyond this, the lift-out sequence ensures everything stays flat even as the clamps move the sheet between cuts. A poor sequence can alter skeleton integrity, which can warp web sections and increase the chances of a part getting caught as it’s being removed.
To prevent this, Mongeau said he alternates the sequence where pieces are parted out and removed, sometimes near the clamps, sometimes away from them (near the front of the machine). “This helps us balance out the weight of that skeleton, so everything stays nice and flat. Again, this is especially important with the laser, which has that narrow kerf.”
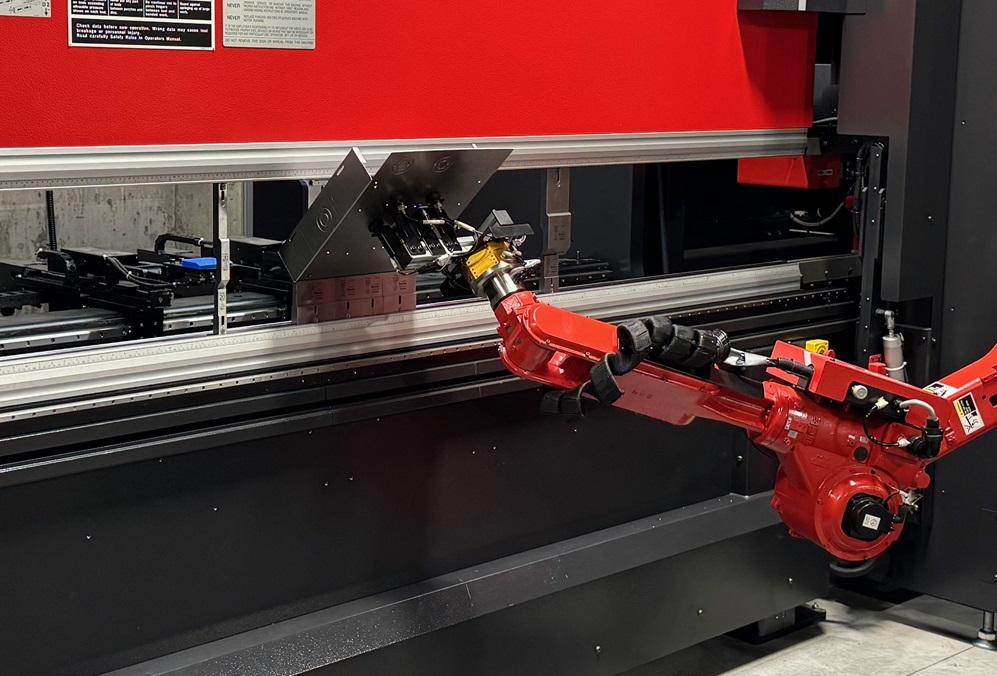
FIGURE 5. A robot forms a precision enclosure. To streamline the bending cycle, every flange, including the small return flanges, was formed without gripper repositioning. Space Age Electronics
At this point, programmers have dialed in nesting to such a degree that material yield has increased significantly. Yes, some parts do need to be tabbed together in mini-nests to ensure reliable removal, but this doesn’t always mean the material yield suffers. Overall, in fact, programmers have found they can make nests with thinner web sections than required for nests destined for a manual turret punch (see Figure 7).
The Transition Continues
2017 began a time of change at Space Age, technologically and culturally. Yes, automation is about augmenting, not replacing, jobs—but tell that to someone whose built a career as a welder or expert brake operator.
“Out of the gate, we worked hard on the cultural aspect,” Mongeau said. “When we started, we heard the concerns that robots were going to take jobs. But then we showed them what the automation could do for them and gave them the bandwidth to tackle more engaging work, the jobs that require an artisan touch. They’re no longer doing our high-volume, repetitive work, and that’s better for them. It makes them more valuable as a fabricator and operator.”
Space Age’s automation journey started in fabrication, but it won’t end there. Other areas of the floor, including the operation’s custom printed circuit board manufacturing, might start seeing some changes.
“And because our overall fabrication capacity has ballooned, we can make things at a grander scale,” Mongeau said. “It has allowed us to be a better provider to existing customers and has allowed us to diversify and enter different markets.”
One big reason Space Age continues to have momentum with automation comes down to process refinement. The company’s strategy has involved a combination of big-picture thinking with extraordinary attention to detail. Material flatness, the state of the skeleton during parts removal in blanking, the effects of gravity on large parts in robotic bending—it all matters, as does the big picture: the need for reliable, scalable sheet metal fabrication to support the rest of the enterprise.
About the Author
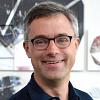
Tim Heston
2135 Point Blvd
Elgin, IL 60123
815-381-1314
Tim Heston, The Fabricator's senior editor, has covered the metal fabrication industry since 1998, starting his career at the American Welding Society's Welding Journal. Since then he has covered the full range of metal fabrication processes, from stamping, bending, and cutting to grinding and polishing. He joined The Fabricator's staff in October 2007.
Related Companies
subscribe now
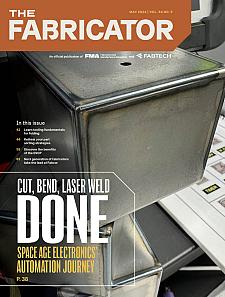
The Fabricator is North America's leading magazine for the metal forming and fabricating industry. The magazine delivers the news, technical articles, and case histories that enable fabricators to do their jobs more efficiently. The Fabricator has served the industry since 1970.
start your free subscription- Stay connected from anywhere
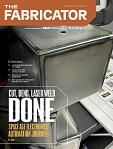
Easily access valuable industry resources now with full access to the digital edition of The Fabricator.
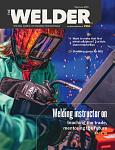
Easily access valuable industry resources now with full access to the digital edition of The Welder.
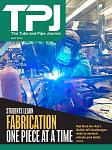
Easily access valuable industry resources now with full access to the digital edition of The Tube and Pipe Journal.
- Podcasting
- Podcast:
- The Fabricator Podcast
- Published:
- 05/14/2024
- Running Time:
- 62:12
Cameron Adams of Laser Precision, a contract metal fabricator in the Chicago area, joins the podcast to talk...
- Trending Articles
What software automation means for custom fabrication
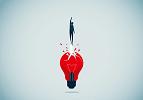
Why employee-owned companies make sense in manufacturing
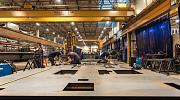
Nucor’s weekly steel price announcement continues to rattle markets
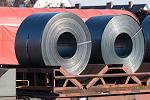
Press brakes, panel benders, and flat blank calculations
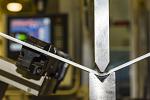
Washington artist creates life-size elk sculptures
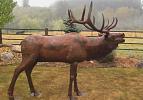
- Industry Events
Laser Welding Certificate Course
- May 7 - August 6, 2024
- Farmington Hills, IL
World-Class Roll Forming Workshop
- June 5 - 6, 2024
- Louisville, KY
Advanced Laser Application Workshop
- June 25 - 27, 2024
- Novi, MI
Precision Press Brake Certificate Course
- July 31 - August 1, 2024
- Elgin,